This post was written for "Portrait of a Kiln," a show of photographs of ceramicists Jesus Minguez, May Wong, Austin Lindsay, Chad Steve and others with the kilns we built, accompanied by our writing and a handful of pots fired in those kilns. The show is curated by Richard Munster on view at FAVO opening Friday, March 1st and on view through that month. Photo by Shoog McDaniel
With modern technology and ancient wisdom combined, we have the means to solve each and every social and environmental problem.
I was introduced to the rocket kiln by Lisa Orr, a ceramicist and permaculturist who lives just outside of Boston, Massachusetts in a town called Northborough. I had been trying to barrel fire terracotta pottery with limited success since 2015. I wanted to make pots that looked ancient; brick-red vessels marked black with smoke, a phenomenon called fire clouding. No matter how much I read about barrel firing and no matter how many YouTube videos I watched of other people doing it, my results were mostly disappointing.
I started working with Lisa through a virtual program called Clay Cohorts last year, and when she learned about my barrel firing woes, she immediately suggested that I build a rocket kiln.
To understand this kiln, we must return to its predecessor, the rocket stove.
Developed in 1980 by Larry Winiarski, the technical director of Aprovecho Research, the stove was meant to eliminate injuries and reduce health risks associated with cooking on open fires by replacing them with experimental wood burning stoves that were more efficient and smokeless. The design of the rocket stove, based on ancient technology such as Roman hypocaust heating systems, is simple and was easily adopted by those in countries such as Guatemala where cooking food over open fire is common.
Lisa got the idea for the rocket kiln when she attended a workshop on rocket mass heaters, a system that uses a similar design as the rocket stove, but instead of cooking food, the generated heat is used to warm indoor spaces. The wondrous thing about rocket stoves and heaters is how little wood it takes to reach high temperatures. In fact, this efficiency, and the speed at which it occurs, creates a potential problem for the firing of ceramics, which I will discuss later. But that rocket mass heater workshop set off a light bulb in Lisa’s head.
She knew that this simple, primitive technology could be used to fire pottery using scrap wood, essentially garbage, for fuel.
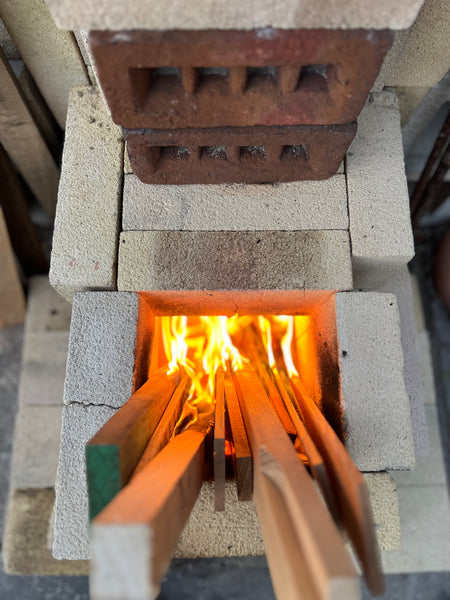
The rocket kiln works best when fed scrap wood such as old, broken pallets or refuse from furniture makers. When I was experimenting with barrel firing, smoke inhalation was a huge problem for me and made the entire process even more discouraging. Building a rocket kiln was an accessible and inexpensive way for me to have an outdoor kiln that eliminated the problem of smoke inhalation altogether.
Meanwhile, I had been collecting clay samples I came across in different locations since 2016. Gray clay from off the beach in Cape Cod that turns a shiny, vitrified brown at cone 5. Yellowish-brown clay from the woods in Louisiana that turns brick red. Greenish clay from Lake Eerie that melts into a puddle of glass when fired mid-range. Early last year, one of my husband’s co-workers brought me a five gallon bucket of clay from a construction site. It was the first time I had more than a handful of foraged clay to work with. It was also around the same time I’d built my new rocket kiln. All of these elements coming together created a new body of work for me, one in which no commercial ceramic products are used.
I dig the clay, dry it in the sun, slake it down in water and push it through a sieve with my hands.
I collect the scrap wood, the sawdust, the seaweed, the Spanish moss. I build each pot by hand with coils. The resulting fired pieces, marked with smoke, are sealed with beeswax. The entire firing process takes anywhere from an hour and a half to three, depending on conditions.
I got all of the elements to build this kiln from Facebook marketplace for cheap including the kiln shell and the fire brick. If you’re patient and lucky enough, you might be able to collect all of the elements you need for free. I am using the kiln to saggar fire my pots, but the possibilities are numerous. Lisa has done cone 10 soda firings in the rocket kiln and I hope to experiment with low-fire soda in the future.
Right now, I still bisque fire my pots in an electric kiln before I saggar fire them in the rocket kiln. That is because of the speed at which rocket kilns increase in temperature. Clay likes to be fired slowly to avoid cracking and explosions from any water that has not fully dried from the pot. Lisa has successfully bisque fired in a rocket kiln, although all of her pieces were smaller and thin-walled. I think that for this kiln to be used in place of electric kilns, the issue of being able to safely bisque fire must be addressed.
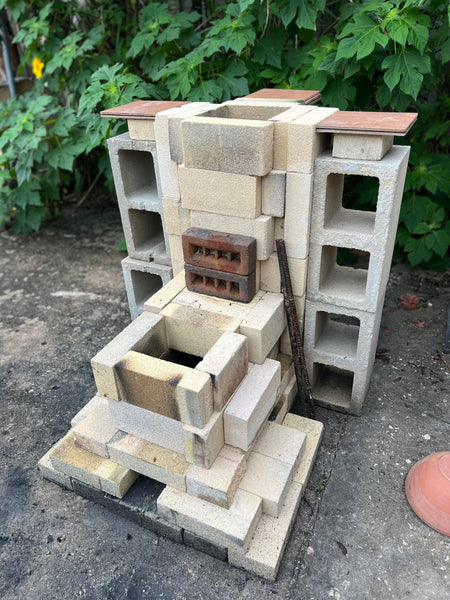
This is why we need more people to build and use rocket kilns: the idea is so new that everyone who uses one helps aid in its advancement. The design plans have already evolved since I built mine last year.
At a time when ceramic equipment is increasingly expensive and many of us are looking for ways to decrease our reliance on fossil fuels, this kiln presents a welcome solution. My hope is that the rocket kiln can create economic accessibility to ceramics and be an environmentally sound firing option for ceramicists everywhere.
Discussion group including pdf with materials list and step-by-step building instructions: The Wood Fired Rocket Kiln Project